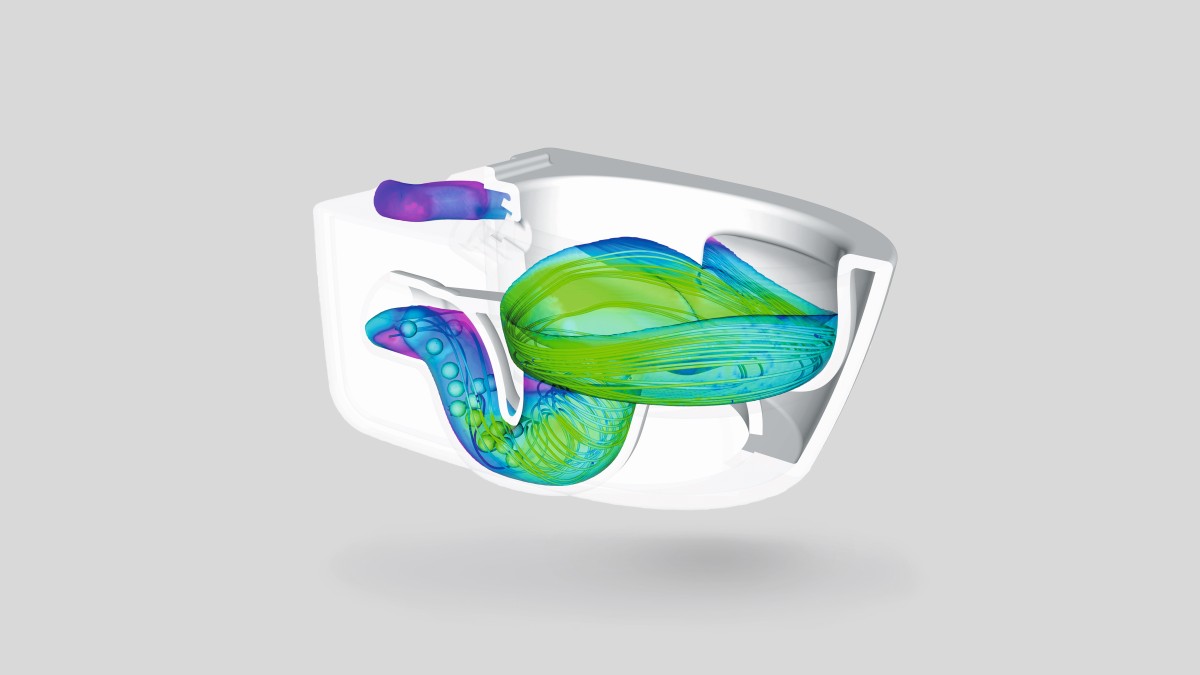
What do a racing car and sanitary products have in common?
They really do have something in common. When developing a new racing car, all the necessary simulations are performed on the computer before the first bodywork is manufactured and tested in the wind tunnel. Things are much the same at Geberit.
Whether a new discharge pipe, trap, WC ceramic appliance or spray nozzle for a shower toilet, a prototype is constructed only after a thorough analysis has been carried out. Before this, we examine all the relevant characteristics on the computer. Like in Formula One, this enables us to make the development process substantially more efficient.
The virtual past life of our products
In specialised simulation programs, we allow virtual water to flow through virtual elements such as spray nozzles, WC pans and traps – and even through entire piping systems. We monitor flows and turbulence as well as the pressure and velocity distribution of the water – and, of course, the development of noise. The sequences shown on screen enable us to optimise the mechanical, flow and acoustic properties of the individual components. The toilet flush, for example, not only has to be thorough, but quiet too. Only then is a testable prototype created by the 3D printer. The prototype then undergoes a range of further tests before the product goes into series production, ready for use in the real world.