Wozu tausende von Prototypen?
Innovationen, frisch gedruckt
1982 beschreibt der Japaner Hideo Kodama als Erster den schichtweisen Aufbau eines 3D-Druckverfahrens. Doch den ersten wirklich brauchbaren 3D-Drucker baut der US-Amerikaner Charles W. Hull 1984. Das ist der Start in eine neue industrielle Ära – auch in der Produktentwicklung von Geberit.
An konkreten Vorstellungen für neue, bessere Produkte fehlt es Geberit nicht. Doch wie erfahren wir, ob diese Ansätze für die Herstellung und für ein Produktleben taugen? Klar ist: Ein Gut-zur-Produktion erfolgt nicht auf der Basis einer Konstruktionsskizze am Bildschirm. Der Entscheid muss handfest sein. Also wird ein neues Produkt oder ein neues Bauteil möglichst real auf Funktionalität und Machbarkeit geprüft. Dazu dienen Prototypen, von denen wir jährlich Tausende in unseren Labors testen. Möglich ist eine solche Stückzahl aber nur dank modernster Technologie.
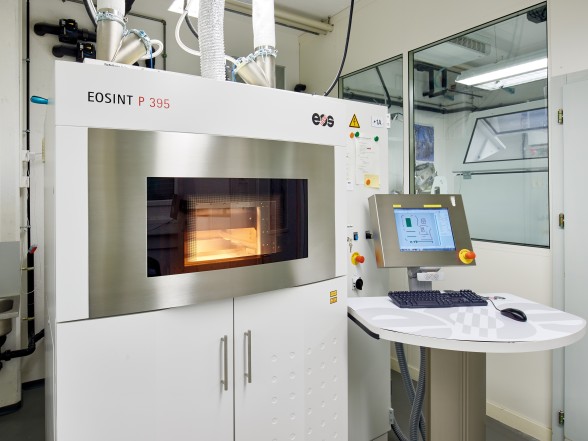
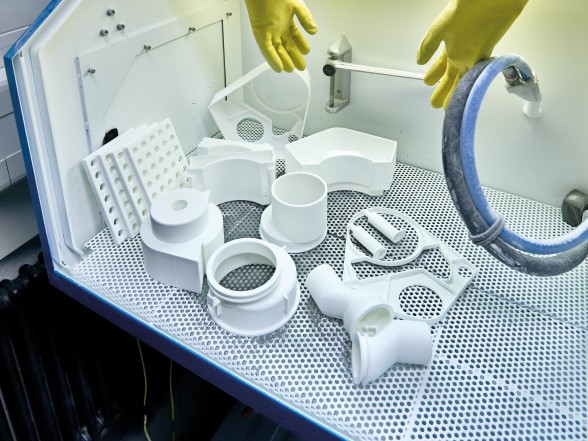
Innerhalb von Stunden
Die Vorgaben für Design und Funktion entwickeln wir anhand von 3D-Modellen im CAD-Programm. Danach geht’s schnell: Musste früher jemand rund zwei Wochen einen Kunststoffblock mechanisch bearbeiten – das heisst fräsen, bohren, ausdrehen, kleben und schweissen –, gelingt das heute digital innerhalb von Stunden. Dies dank additiver Verfahren wie Lasersintern und 3D-Druck, die wir seit rund zehn Jahren anwenden.
Wie «additiv» funktioniert? Beim Lasersintern wird der Werkstoff als dünne Pulverschicht auf eine Plattform aufgetragen. Ein Laserstrahl schmilzt das Pulver entlang der CAD-Daten des Bauteils, worauf sich diese Stellen mit den nächstunteren verbinden. Danach senkt sich die Platte um eine Schichthöhe und der Prozess wiederholt sich. Am Ende wird das fertige Stück aus seinem Pulverbett herausgelöst. Beim 3D-Druck hingegen wird für verschieden harte Werkstoffe statt Pulver Flüssigkeit aufgetragen. Diese wird mit UV-Licht gemäss den Konstruktionsdaten punktgenau gehärtet und schichtweise verbunden, bis das Bauteil «ausgedruckt» ist.
Schneller am Markt
Für Langzeittests von hoch beanspruchten Produkten wie beispielsweise Verbindungsstücken von Rohrleitungssystemen werden die Prototypen nach wie vor im Originalverfahren und mit Originalwerkstoffen hergestellt. Doch für andere Produkte und Bauteile mit komplexer Formgebung wie etwa Spülventile, Siphons oder WC-Sitze sind die Vorteile additiver Verfahren enorm. So lassen sich wesentlich mehr Varianten herstellen und testen. Und auch die Entwicklungszeit kann um bis zu 20 Prozent verkürzt werden.
Noch ist die Produktionsgeschwindigkeit der additiven Verfahren limitiert. Auch die Auswahl an einsetzbaren Werkstoffen ist im Kunststoffbereich sehr begrenzt. Sicher ist, dass sich dies in den nächsten zehn Jahren deutlich verbessern wird. Spätestens dann wird diese Technologie auch für die Herstellung gewisser Endprodukte höchst interessant. Geberit ist bereit.