From 17 to 1
Creating a new flush valve
Two new production lines for the flush valve type 212 in Pfullendorf (DE) offer maximum flexibility. This not only applies to production, but also to some other aspects that you wouldn’t think were possible on a piece of equipment weighing several tonnes.
They are called Linda, Marie or Ramona and share their names with players from the German and the Swiss women’s national football teams. While scoring goals isn’t on the agenda, perfect teamwork is essential when manufacturing the new flush valve type 212. These 30 orange robot arms are an integral part of the two production lines on the flexible assembly system in Pfullendorf (DE).
High-precision in-house construction
Since the start of the project, the system has been the responsibility of Fabian Hiller (35), GPS Project Engineer in Pfullendorf. Under his direction, the flexible assembly system was then designed and developed on time and on budget within one and a half years. This was thanks to an in-house team made up of designers, plumbers, control technicians and IT specialists. Only specific components such as the robot arms were purchased elsewhere. “The goal was to optimise the production time of the flush valve and reduce the complexity to minimise the workload on the employees,” sums up Fabian Hiller. With a production time of just 7.5 seconds per flush valve, this test has been passed with flying colours.
Maximum flexibility
When running at full speed, the two lines can manufacture several thousand flush valves every day. To do this, three employees are required. They operate the system, fill it with the 17 different individual parts and then remove the finished flush valves. However, it is possible to operate the flexible assembly system with just one person. The output is then lower as a result. This also means that the staff can be divided up better between the different production lines across the entire facility. “This flexibility is one of the biggest strengths of the production lines and makes them very popular across the company,” comments Fabian Hiller.
Ready for the future
Another feature of the 30-metre-long flexible assembly system is its modular design. This means that the system can be set up even more quickly.
The modular design offers another advantage: the system is ideally suited for relocation. This is because a new production hall will go into operation in Pfullendorf in 2024. The flexible assembly system will take its permanent place there.
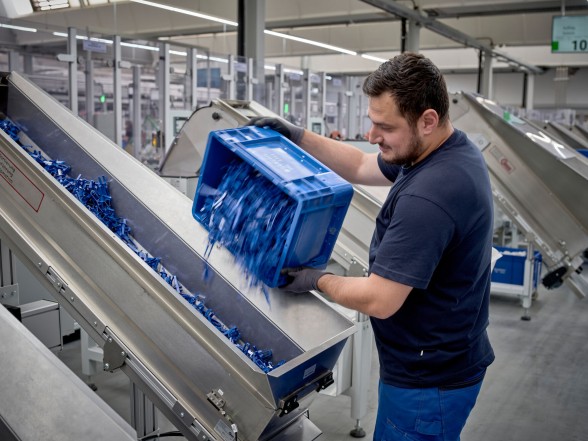
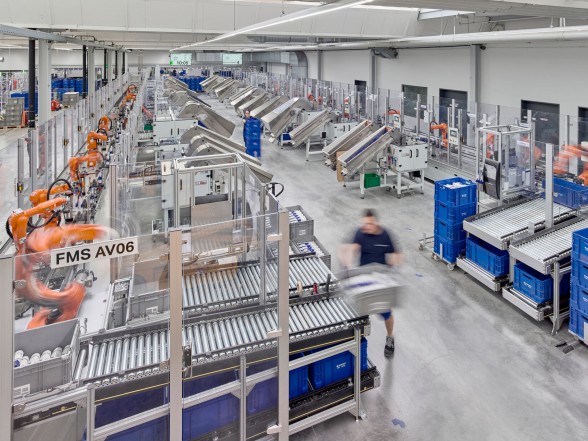