From the kitchen to the ceramics plant
In Finland, practical experience is what counts
Unconventional careers such as those of Johan Pihlström and Johan Malmsten are part of everyday life in Ekenäs (FI). A willingness to learn is more important to the HR department than an impressive CV. This approach really pays off.
Over 25 years ago, Johan Pihlström hung up his apron in favour of a set of overalls at the ceramics plant in the Finnish town of Ekenäs. Then aged 19, the trained chef worked at the plant to earn some money before starting catering college. “I was young and liked the money,” he says with a smile.
He decided to stay: “The good working atmosphere, my colleagues and the chance of taking on new tasks really won me over.” Today, he is sought after as a specialist for the latest generation ofpressure casting machines used for manufacturing ceramic appliances. However, he continues to follow his passion for cooking in his free time.
Learning by doing
Like Johan Pihlström, many of the employees now work in different areas to those they trained in. This is also due to the transformation of the plant over time. “We used to make ceramic appliances by hand, but now the employees operate machines instead,” explains Camilla Karlsson, HR Manager in Ekenäs. Learning by doing is the maxim here – seeing how things work in practice instead of on paper.
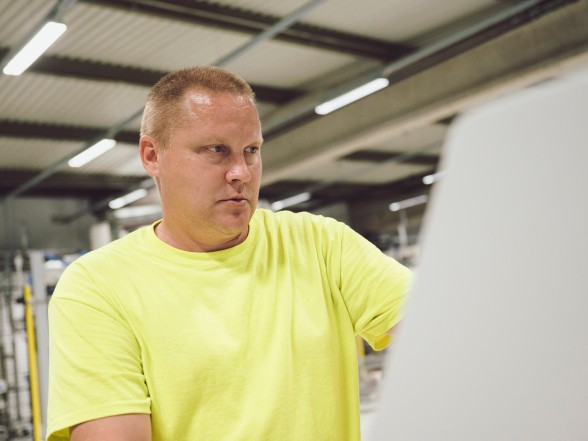
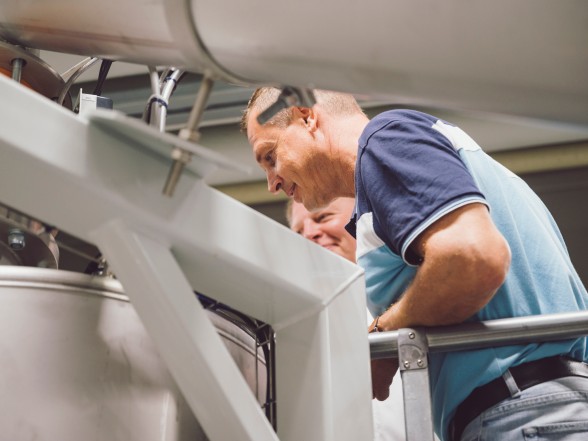
Born of necessity
People from different careers are a focal point during recruitment. This was born of necessity, as there are no further education options in ceramics nor other manufacturers of ceramic appliances in Finland. Recruitment is therefore a more pragmatic affair than in other places. “We are looking for people with technical skills, such as those from the automotive or mechanical engineering industry,” explains the HR Manager.
Another source is the construction industry, as was the case with Johan Malmsten. Due to a recession in the branch, the newly trained master builder started work at the ceramics plant almost 30 years ago. His goal was to find a short-term alternative to tide him over during the crisis. But, as has been seen time and time again, things didn’t work out that way. “I enjoyed the work so much that there was no longer any reason to change jobs,” he explains. Instead of the construction site, he now organises the processes in the Ekenäs Tooling Centre.
The approach appears to be paying off: the average length of service among the some 180 employees in Ekenäs is an impressive 18 years – and as high as 20 years in production.