It separates the wheat from the chaff
Metal detector in use
Only in use since the beginning of 2023, an automatic detective in the warehouse for plastic raw material is doing a clean job. This is particularly in line with the aim of increasing the proportion of recycled plastic.
Admittedly, you rarely see it in action. On average, the metal extractor spits out around 100 grams of contaminated material for every 10 kilograms of plastic regranulate. It can take several cycles before a jolt goes through the pipe and a handful of granulate ends up in the waste bag. The particles separated out are usually tiny: they are metal particles enclosed in plastic granules, loose pieces of metal or shavings, broken screen wires or even non-metallic foreign materials. The metal extractor finds them all.
There is no clean waste
This benefits the use of recycled plastic in particular. Recycled material is not only cheaper than virgin material; its production requires around 80% less energy and causes up to 80% less CO2 emissions. However, the ecologically valuable post-consumer recyclate in particular does not achieve the purity levels of virgin material. Obtained from electronic waste or packaging film for agricultural products, for example, the granulate supplied always contains small foreign bodies, organic fibres or metal particles.
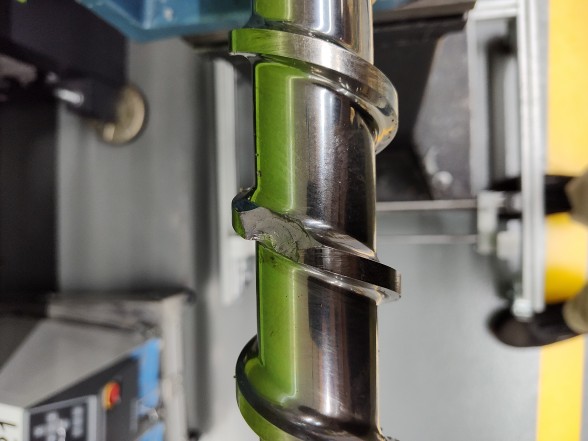
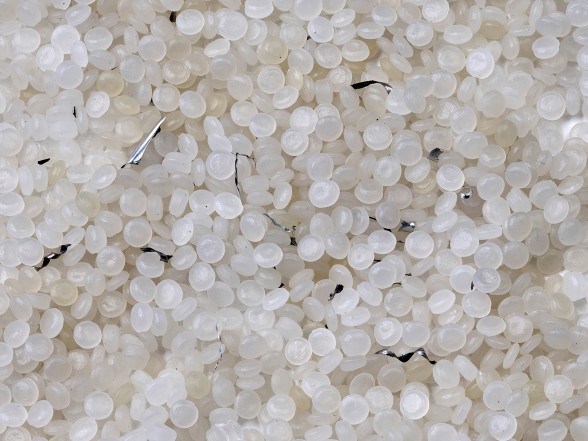
Small weak point – big problem
As small as they may be, the problems they cause are huge. At the Jona plant alone, the uninvited guests caused damage to machines and tools amounting to around CHF 60,000 (Euro 63,000) in 2022: they clogged nozzles in the injection moulding tool, increased wear on machines or magnetised to form large lumps in the material hopper of the injection moulding machines.
This is now history: A total of five metal extractors check the purity of the raw material delivered to the Jona plant. The result: no more damage costs that could have been caused by foreign materials in the post-consumer granulate for a year now.
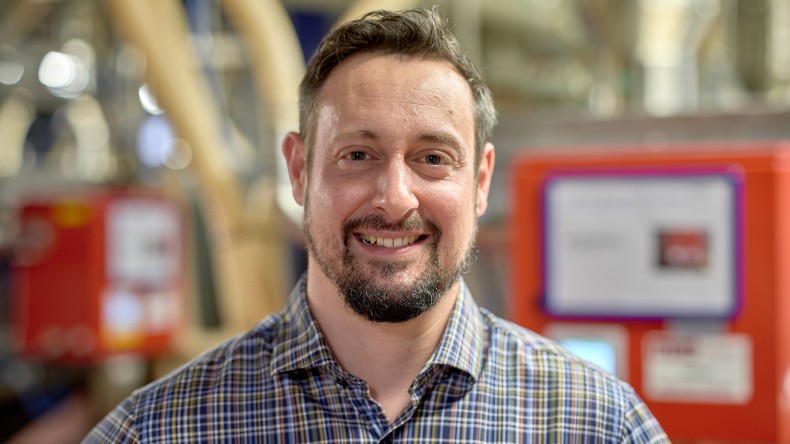
Turning waste into raw material
Geberit wants to gradually increase the proportion of recycled plastic. In packaging, for example, recycled plastic should account for around 30% of the total plastic processed by 2030. Post-consumer recyclate, i.e. material produced from consumer waste, is particularly important from an environmental perspective. Geberit has been using this material for some time. It is used to make mounting frames for actuator plates or components such as the flush guide for the iCon toilets, parts of the flush valve 240 or the fill valve 333. The Jona plant (CH) alone processes 530 tonnes of ABS recyclate (acrylonitrile butadiene styrene) every year, and the Group as a whole processes around 800 tonnes. In addition, recycled PE-LD and PP plastic is used to produce various protective caps and lids.
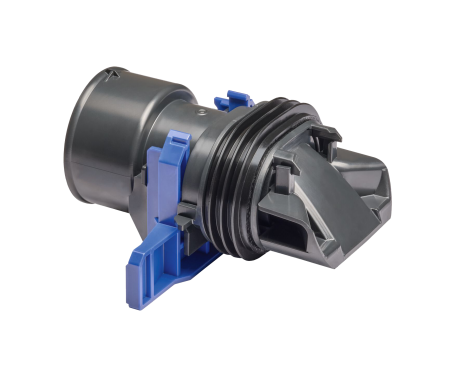