Holograms for efficiency
Digital aids in production
Two Geberit plants have tested out hologram technology over the past few years – and have come to some very different conclusions.
With new digital technologies launched seemingly every day, putting them through their paces in everyday work is usually the only way of finding out which ones are useful. Geberit Produktions AG (GPAG) in Rapperswil-Jona and the Polish plant in Ozorkow both simultaneously tested out the HoloLens, a device that process engineer Silvio Gächter from GPAG calls a “digital facilitator”.
HoloLens is a type of monitor that is worn on the head of the operator. At the front is a pair of glasses with a special coating that makes holograms appear as if by magic. These holograms can be seen by the operator, but are invisible to others. By moving their hands in the air, the operator can move, click on and enlarge the holograms – similar to when using a touchscreen. The actual surroundings remain visible at all times.
Service by remote control
This technology can be a real benefit to the plants. A malfunctioning machine needs to be looked at by a service technician. However, instead of making the journey to the plant, they can see things digitally thanks to the HoloLens. A member of staff puts on the glasses and calls the technician via Microsoft Teams. Regardless of where they are, the technician sees the same things on screen as the person on site. This then allows the specialist to guide the on-site staff through the maintenance process remotely.
Przemysław Skwierczyński, Senior Technology Engineer in Ozorkow, comments: “This type of service was absolutely critical during the COVID-19 pandemic.” Poland temporarily closed its borders, meaning service technicians from abroad were unable to enter the country. This posed some major challenges for the plant in Ozorkow, which operates many different machines from international manufacturers.
At the same time, the plant in Jona was also putting the HoloLens through its paces. While it proved useful during the pandemic, it was mothballed shortly thereafter. “Simple issues were able to be solved over the phone thanks to the extensive injection moulding expertise in the plant,” explains Silvio Gächter. “If more complex solutions were required, then the service provider had to be on site anyway.” As a result, the HoloLens project was not followed up on.
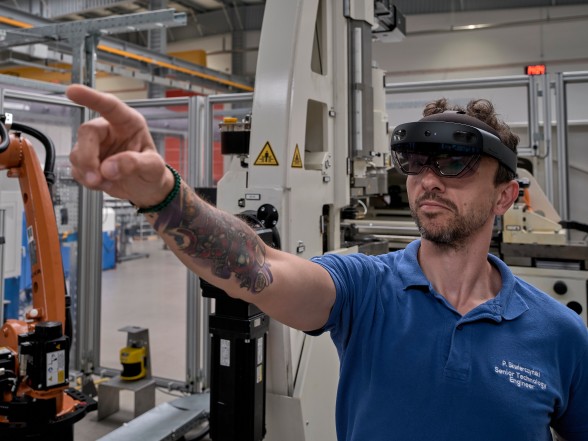
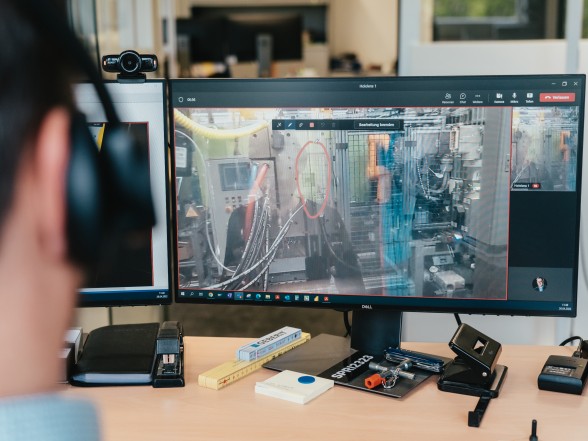
Fewer journeys, lower costs
This technology is still in use in Ozorkow. According to Przemysław Skwierczyński, the majority of maintenance work on three machines from Western Europe is currently being carried out using the HoloLens. Thanks to the HoloLens, an expensive on-site visit by technicians can often be dispensed with. “As this maintenance method has now become established, we can include it in the contract when purchasing new machines. Maintenance work is usually carried out digitally at our plant – this is the future.”