New hot stuff
Saving energy and CO2
A kiln that can be loaded on two levels does the work of three tunnel kilns at the Portuguese ceramics plant – and saves an enormous amount of energy and CO2.
Chairman of the Board of Directors Albert M. Baehny, CEO Christian Buhl and Head of Group Executive Area Operations Martin Ziegler ceremoniously unveiled the plaque commemorating the inauguration of the new kiln at an indoor temperature as high as 37°C. Pleasantly cool compared to the 1,200°C that will soon prevail inside the kiln when it goes into operation.
Productive burner
The 120 metre long facility is not only impressive on the outside. “The new tunnel kiln replaces three outdated models,“ explains Managing Director Mário Cunha.
The Carregado team is visibly proud of the new kiln: “The first at Geberit that can be loaded on two levels“. With this, it has a greater capacity than the old systems combined, 1.3 million units per year instead of 900,000. That’s over 3,500 ceramic appliances fired every day.
3,500 tonnes of CO2 saved per year
The energy-efficient kiln achieves all this with 40 per cent less energy in the form of gas compared to the old units. As a result, the plant saves 3,500 tonnes of CO2 every year.
Mário Cunha also appreciates the side effect: “The new solution requires less space. It frees up 2,500 square metres in the plant.“ Around 200 cars could be parked in this space.
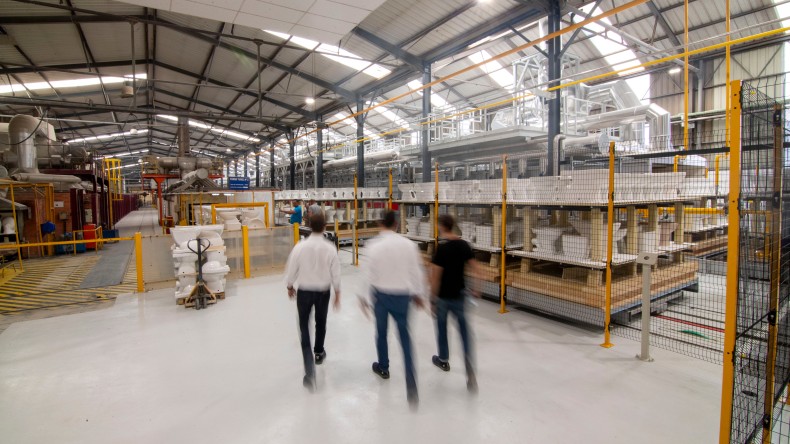
Recovering energy
The new system can do even more: energy can be recovered from the hot exhaust air from the cooling zone. Diogo Gameiro, GPS Manager (GPS: Geberit Production System), says: “With the additional kilowatt hours, we will be able to operate some of the boilers, dryers and climatization systems in future and use less gas.“
60 trucks with material
Diogo Gameiro is responsible for the challenging project. “I've been working in project management for almost ten years, but this was a new level,“ he says. In addition to the budget and schedule, the logistics were a particular challenge. “Our supplier would have preferred to deliver all the material for the new kiln to us in one batch. We’re talking about more than 60 fully loaded trucks!“ As there was no space on the site, the team had to receive the deliveries spread out over months and meticulously plan each day in advance.
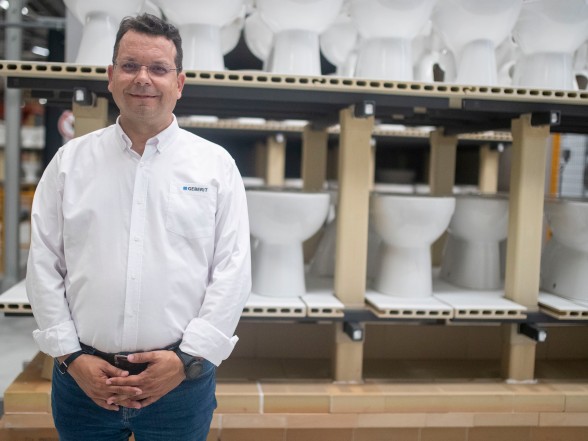
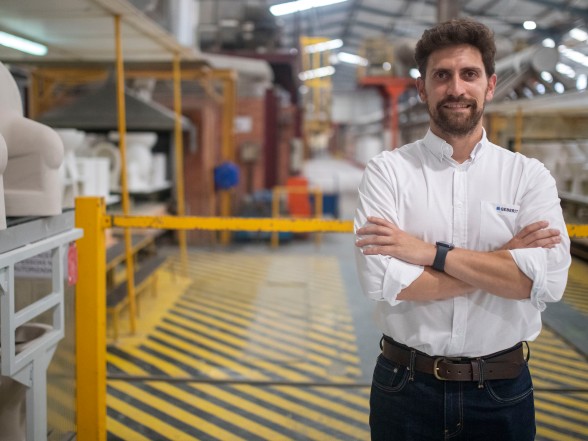
Geberit CO2 strategy
The energy-efficient double-deck kiln is an important component of Geberit’s CO2 strategy. The aim is to reduce Group-wide CO2 emissions in relation to currency-adjusted net sales by 5% each year. If Geberit achieves this goal, the company will emit around 80% less relative CO2 emissions in 2035 than in 2015, when the ceramics business was acquired.