Relief for man and woman
Ergonomics in the ceramics plants
Handling high weight loads was part of the daily routine of many production employees in the ceramic plants. Since the acquisition of the ceramics business, Geberit has invested in automation processes and lifting aids. Around 650 employees now have it easier.
On average, a toilet weighs between 20 and 30 kilos, a washbasin between 10 and 20 kilos. A double washbasin can weigh up to 60 kilos. Each of these ceramics is lifted, repositioned and turned over several times until it leaves the factory finished and packaged. Ergonomic workplace design is of central importance, especially in factories with a large proportion of manual work and a high product weight. Back problems and other musculoskeletal disorders can affect production workers over time.
Protecting health
Since the acquisition of the ceramics business in 2015, Geberit has been continuously investing in automation and ergonomic aids in the ceramics plants. By the end of 2020, almost 200 workplaces in the ceramics plants with a high proportion of manual work had been equipped with various lifting aids or ergonomically redesigned. Around 650 people will benefit from this.
“Zero lifting“ in Gaeta
The Italian ceramics plant in Gaeta serves as a role model for many ceramics plants with a high proportion of manual work. Since 1998, the factory has been introducing lifting aids step by step, department by department. From the casting department to the packaging department, no one has to use physical force any more to process and finish the ceramics. Cranes, lifting and tipping equipment, vacuum grippers, pneumatic and electric lifting devices ensure that, despite a traditionally manual production method, the goal of “zero lifting“ has been achieved throughout the entire production process.
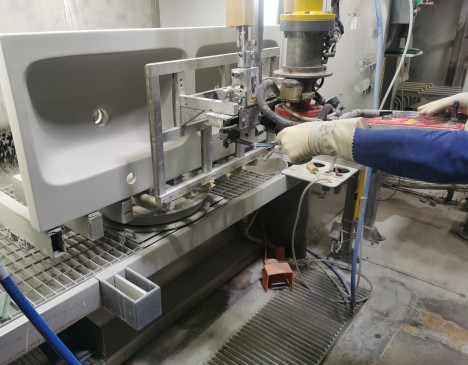
Automatic raw material dosing
“Zero Lifting“ is also the goal at the two Polish ceramic plants in Kolo and Wloclawek. In Kolo, an automatic system now makes the dosing of raw materials much easier. Until now, employees have hoisted the heavy sacks of raw material onto the loading platforms and emptied them there. The changeover to an automated raw material dosing system not only reduces the daily load lifting, but also the exposure to the dust while emptying the sacks.
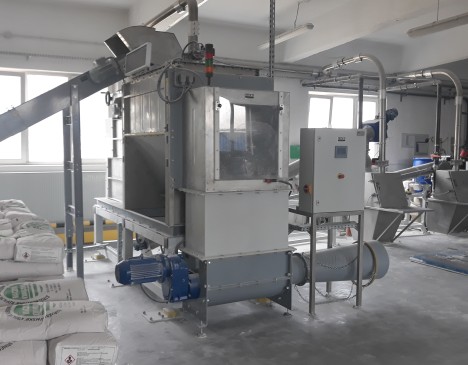