Thousands of prototypes – what for?
Innovations, freshly printed
In 1982, the Japanese engineer Hideo Kodama becomes the first person to describe the layered structure used in 3D printing. However, the first truly usable 3D printer is built by the American inventor Charles W. Hull in 1984. This is the start of a new industrial era – and also a new era in product development at Geberit.
Geberit is not short of concrete ideas for new, better products. But how do we find out whether these ideas are suitable for manufacturing and beyond as an actual product? One thing’s for sure: Production approval is not issued on the basis of a design sketch on the screen; something more tangible is needed. A new product or a new component is therefore tested for functionality and feasibility under the most realistic conditions possible. This is where prototypes – of which we test thousands in our labs each year – come into play. However, such an impressive quantity is only possible thanks to state-of-the-art technology.
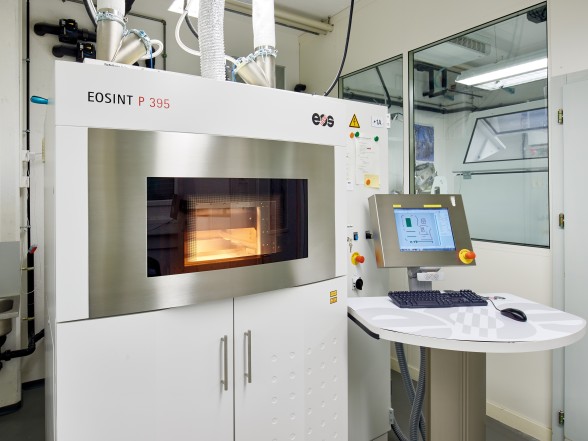
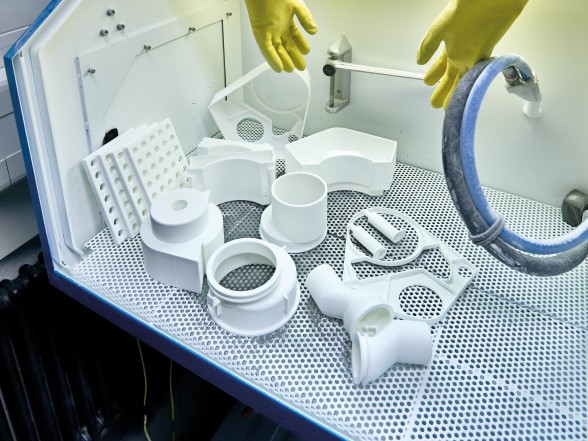
In just a matter of hours
We develop the specifications for design and functionality using 3D models created in the CAD program. Things go fast from this point on. While someone used to have to spend around two weeks machining a plastic block – milling, drilling, turning, bonding and welding – this can now be done digitally in just a matter of hours. This is all thanks to additive processes such as laser sintering and 3D printing, which we have been using for around ten years now.
How does “additive” work? In laser sintering, the product material is applied to a platform in the form of a thin layer of powder. A laser beam melts the powder at points defined by the component’s CAD data, whereupon these points bond with those directly underneath. The platform is then lowered by the thickness of one layer and the process is repeated until the item is finished and removed from the powder bed. With 3D printing, on the other hand, liquid is applied instead of powder for product materials of different hardnesses. This liquid is hardened precisely using ultraviolet light in accordance with the design data and joined together layer by layer until the component is “printed”.
Quicker on the market
The prototypes for the long-time testing of products that are subject to great stress, such as connecting pieces in piping systems, are still made using the original process and the original product materials. However, the benefits of additive techniques are enormous for other products and components with complex designs, such as flush valves, traps and WC seats. A significantly larger number of versions can be made and tested, for example, and the development period can also be reduced by up to 20 per cent.
There is still room for improvement when it comes to the production speed of additive techniques, and the choice of usable product materials is also extremely limited in the plastics sector. What is certain is that this situation will improve considerably over the next ten years, by which time this technology will also be an interesting solution for the manufacture of certain end products. Geberit is ready.