Versatility and blue powder
Doreen Schrön-Müller from Lichtenstein plant (DE)
Quality, safety, environmental management and a major construction project in between: Doreen Schrön-Müller is a woman for all occasions at the Geberit plant in Lichtenstein (DE).
It measures 74 metres and is therefore longer than a football pitch is wide. The new powder coating machine for the Duofix production line in Lichtenstein (DE), which is currently under construction, is a giant. Doreen Schrön-Müller knows how to plan such a behemoth.
She has been working at the plant in Saxony, which opened in 1992, for over 30 years and is considered a jack-of-all-trades. She is responsible for quality, occupational safety and environmental management. Aside from that she’s always happy to supervise major projects “on top“, as she says.
Three plants planned
This began early on. As quality manager, she meticulously monitored the production processes for the Duofix, which was launched in 1996. This included powder coating, which was initially carried out by an external partner. Doreen Schrön-Müller was therefore the most competent internal person when the process was brought in-house – and has been planning powder coating systems together with the Head of Process Engineering ever since.
The first plant has long since disappeared. The second is still producing today. The new system is now the third. And it is proving to be more challenging than the previous ones, as it is embedded in a fully automated process. Robots transfer the welded frames to the system and remove them after coating. This requires maximum precision in the planning and construction of the system.
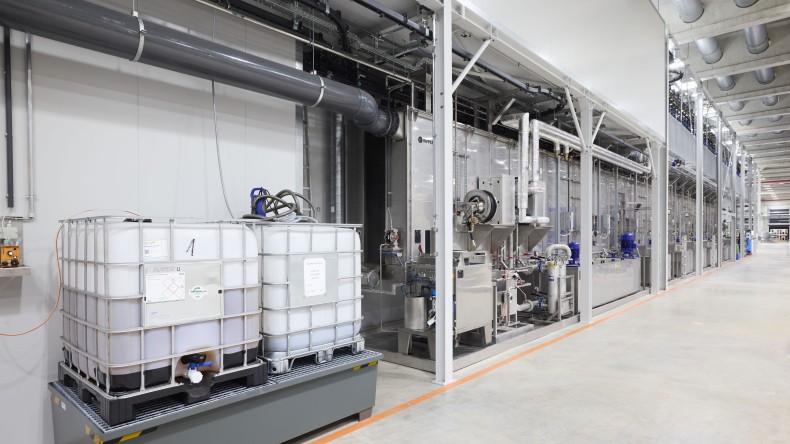
“My glasses as an environmental officer have paid off in the planning“, she says. One example: After the blue powder has been applied, the Duofix frames are fired in a kiln. Thanks to various heat recovery stages, the heat is reused within the plant – making the process more environmentally friendly.
Accident statistics improved
As soon as the new line is ready for production, Doreen Schrön-Müller will return to her core tasks. In particular, she is constantly concerned with the accident statistics. “We have recently achieved enormous improvements.“ Particularly noteworthy is the fact that the accident rate involving forklift trucks fell to zero in 2023. “On the one hand, this is thanks to the introduction of driverless transport systems – they circulate accident-free. On the other hand, the workforce is much more aware.“ This is because every accident at work is meticulously investigated.
For her, the variety of topics in her job is a benefit – even if it sometimes leads to overtime. “I always enjoy getting up in the morning. I sympathise when something doesn't work and am very quick to find solutions. But to be honest: most of the time, everything goes very well.“